Measuring vibration in mechanical systems is crucial for ensuring optimal performance and longevity. Accurate vibration measurement helps in identifying potential issues before they become severe.
Vibration occurs in mechanical systems due to various factors, such as imbalances or misalignments. To measure these vibrations, specific tools and techniques are employed. Understanding how to measure vibrations can help maintain machinery health and prevent unexpected failures. In this blog post, we’ll explore the methods and tools used for vibration measurement.
We’ll also discuss why this practice is essential for any mechanical system. Whether you’re a professional or a hobbyist, learning these techniques can save time and money. So, let’s dive into the world of vibration measurement and learn how to keep your mechanical systems running smoothly.
Introduction To Vibration Measurement
Hey friends, today we’ll talk about measuring vibration in mechanical systems. Sounds technical, right? But don’t worry, I’ll break it down into simple steps. Understanding vibration is like listening to the heartbeat of a machine. It tells you a lot about its health. Let’s dive into why measuring vibration is important and where it is used.
Importance Of Vibration Measurement
So, why measure vibration? Good question. Imagine you’re driving and your car starts shaking. You know something’s wrong. Similarly, machines vibrate when they’re not working well. Measuring vibration helps us:
- Detect problems early
- Prevent breakdowns
- Save money on repairs
Think of it as a health check-up for machines. Catching problems early can save a lot of trouble later.
Applications In Mechanical Systems
Vibration measurement is used in many places. Here are a few examples:
- Factories: Machines in factories can wear out. Measuring vibration helps keep them in good shape.
- Cars: Mechanics use vibration measurement to find out what’s wrong with your car.
- Buildings: Even buildings can have vibrations. It helps engineers keep them safe.
These are just a few examples. Almost any machine or structure can benefit from vibration measurement.
Measuring vibration is like having a stethoscope for machines. It helps us find problems early and fix them before they get worse. Whether it’s in a factory, a car, or a building, vibration measurement is a valuable tool. Stay tuned for more on how to actually measure vibration in our next section!
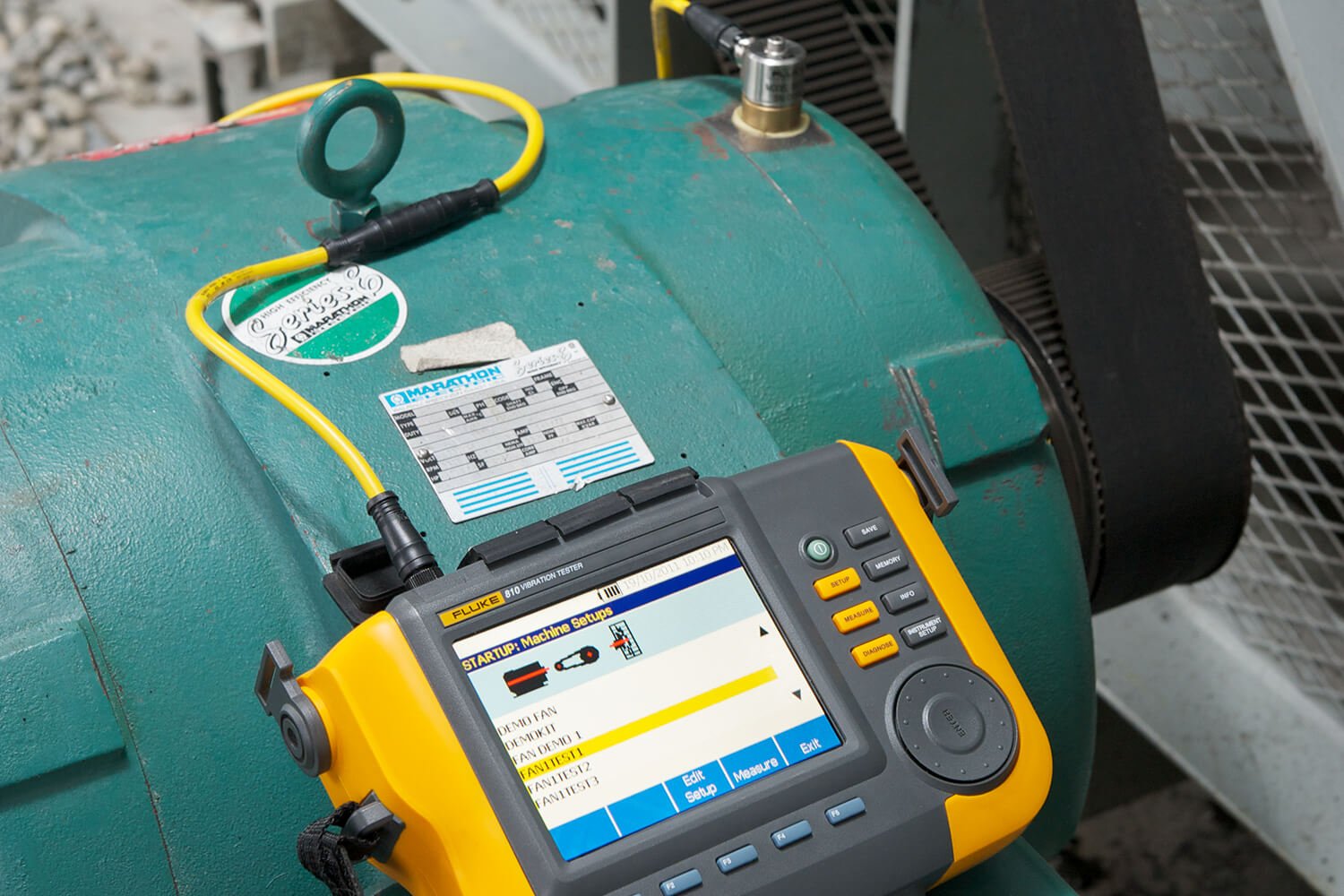
Credit: www.fluke.com
Basic Concepts Of Vibration
Understanding the basic concepts of vibration is essential for measuring vibration in mechanical systems. Vibration can affect the performance and lifespan of machinery. By grasping the core principles, you can monitor and manage vibrations effectively. This section will cover vibration frequency, amplitude, and phase.
Vibration Frequency
Vibration frequency refers to how often an object vibrates within a specific time period. It is measured in Hertz (Hz). One Hertz equals one cycle per second. Frequency indicates the vibration’s speed. Higher frequencies mean more rapid vibrations. Lower frequencies indicate slower vibrations. Knowing the frequency helps in identifying potential issues in mechanical systems.
Amplitude And Phase
Amplitude measures the vibration’s strength or intensity. It shows how far an object moves from its rest position. Higher amplitudes indicate stronger vibrations. Lower amplitudes mean weaker vibrations. Monitoring amplitude is crucial for assessing machinery health.
Phase describes the vibration’s position within its cycle at a specific time. It is often measured in degrees. Phase differences between parts can cause destructive interference. This can lead to increased wear and tear. Understanding phase helps in synchronizing mechanical components.
Types Of Vibration
Hey there! Today, we’re diving into an important topic for anyone dealing with mechanical systems. That’s right, we’re talking about vibration measurement. Understanding the types of vibration is essential for effective measurement. There are two main types: free vibration and forced vibration. Let’s break them down, shall we?
Free Vibration
Free vibration occurs when a system vibrates on its own after being disturbed. Imagine you have a swing. You give it a push, and it keeps moving back and forth all by itself. That’s free vibration. The system isn’t getting any more energy from outside.
Here are some key points about free vibration:
- It happens naturally after an initial force.
- No continuous external force is applied.
- The system will eventually stop due to damping (like friction).
Think of a guitar string. Pluck it, and it vibrates freely. Over time, it stops because of air resistance and internal friction.
Forced Vibration
Now, let’s talk about forced vibration. This type happens when an external force keeps acting on the system. Imagine a washing machine. When it’s running, it shakes because of the motor inside. That’s forced vibration.
Here are the main points for forced vibration:
- It requires a continuous external force.
- The system vibrates at the frequency of the external force.
- If the force stops, the vibration stops too.
Think of this like a kid on a swing, but this time you keep pushing. The swing moves at the frequency of your pushes. Stop pushing, and the swing stops swinging.
Understanding these types of vibrations helps us measure them better. For example, if you know a machine has forced vibration, you can focus on the source of that external force. And if it’s free vibration, look at the initial disturbance. Simple, right?
So, next time you’re dealing with a vibrating system, just remember these two types. Free and forced. It’ll make everything much clearer!
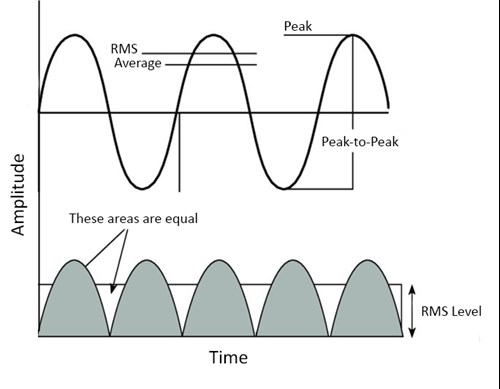
Credit: www.metrixvibration.com
Common Vibration Measurement Tools
Measuring vibration in mechanical systems is crucial for maintenance and performance. Various tools help in detecting and analyzing vibrations. These tools offer precise data for effective solutions. Let’s explore some common vibration measurement tools.
Accelerometers
Accelerometers are popular for measuring vibrations. They are small and easy to attach. These devices convert mechanical vibrations into electrical signals. Engineers use these signals to analyze vibration patterns. Accelerometers are reliable and provide accurate readings. They are suitable for a wide range of applications. From small machines to large industrial equipment, accelerometers are versatile.
Laser Vibrometers
Laser vibrometers are advanced tools for non-contact vibration measurement. They use laser beams to detect vibrations on surfaces. These devices are highly accurate and sensitive. Engineers prefer laser vibrometers for detailed analysis. They are ideal for delicate or hard-to-reach components. Laser vibrometers provide precise data without physical contact. This makes them perfect for high-precision tasks.
Choosing The Right Sensor
Choosing the right sensor is essential for measuring vibration in mechanical systems. The sensor you choose impacts the accuracy and reliability of your data. There are several factors to consider. Two of the most important are sensitivity and range, and environmental considerations.
Sensitivity And Range
Sensitivity refers to a sensor’s ability to detect small vibrations. High sensitivity is crucial for detecting minor changes. It helps in identifying potential issues early. Range, on the other hand, is the maximum vibration level the sensor can measure. Ensure the sensor’s range matches your system’s vibration levels. A sensor with an appropriate range provides accurate readings. Always check the specifications before choosing a sensor.
Environmental Considerations
Environmental factors can affect sensor performance. Temperature, humidity, and dust levels play a role. Choose a sensor that can withstand your system’s environment. For high-temperature areas, select a heat-resistant sensor. In dusty or humid environments, opt for a sealed sensor. This ensures the sensor remains functional and accurate. Always consider the operating environment when selecting a sensor.

Credit: www.sciencedirect.com
Setting Up The Measurement System
Hey friends, today we’re diving into the basics of measuring vibration in mechanical systems. We’ll focus on setting up the measurement system. It might sound tricky, but with the right steps, it’s pretty straightforward. Let’s break it down, so you can get your system up and running smoothly.
Mounting Sensors
The first step? Mounting your sensors. Think of sensors like the eyes and ears of your system. They need to be in the right spot to pick up the right signals. Here’s what to keep in mind:
- Choose the right location: Place the sensor where the vibration is strongest. This is often near bearings or gears.
- Secure the sensor: Use screws or adhesive to make sure the sensor doesn’t move. If it moves, your data won’t be accurate.
- Check alignment: The sensor should be aligned with the direction of the vibration. Imagine trying to listen to a whisper with your ear plugged – it just doesn’t work!
Cable Management
Now, let’s talk about cable management. It’s like organizing your desk – if it’s messy, you can’t find anything. Here’s how to keep your cables in check:
- Use cable ties: Bundle cables together to keep them neat. This prevents them from tangling.
- Avoid sharp bends: Bending cables sharply can damage them. Think of it like bending a straw too much – it just breaks.
- Keep cables away from heat: High temperatures can damage cables. Place them away from engines or other hot areas.
Remember, good cable management not only looks nice, but it also ensures reliable data. If cables are damaged or loose, your readings will be off.
Setting up the measurement system may seem complex at first, but with these simple steps, you’ll be well on your way. Follow these tips to ensure your sensors and cables are set up correctly, and you’ll get accurate vibration data every time.
Data Acquisition And Analysis
Data acquisition and analysis are crucial for measuring vibration in mechanical systems. Accurate data collection ensures reliable analysis. This helps in understanding the health of mechanical systems. Different techniques are used to gather and interpret vibration data.
Sampling Rate
The sampling rate is the number of data points collected per second. A higher sampling rate captures more detailed vibration signals. This is vital for analyzing high-frequency vibrations. Choosing the correct sampling rate affects the accuracy of your data.
Signal Processing Techniques
Signal processing techniques refine raw data. They help in identifying patterns and anomalies. Fourier Transform is a common method. It converts time-domain data to frequency-domain data. This makes it easier to identify specific vibration frequencies. Filtering techniques remove noise from the data. This ensures that only relevant information is analyzed.
Interpreting Vibration Data
Hey there! Ever wondered how to interpret vibration data from mechanical systems? It might seem tricky at first, but with a bit of guidance, you’ll get the hang of it. Interpreting this data helps us understand the health of machinery. It’s like getting a check-up for your car to ensure everything’s running smoothly. Ready to dive in? Let’s go!
Identifying Common Patterns
First, let’s talk about identifying common patterns in vibration data. Think of it like looking for clues in a mystery. Each pattern tells a different story about what might be going on inside the machine. Here are some common patterns to watch for:
- High-Frequency Vibrations: Often indicate issues with bearings or gears.
- Low-Frequency Vibrations: Can suggest problems with alignment or balance.
- Intermittent Vibrations: Might mean something is loose or not properly secured.
By understanding these patterns, you can start to piece together what’s happening inside the machine. It’s like being a detective!
Diagnosing Mechanical Issues
Once you’ve identified the patterns, the next step is diagnosing mechanical issues. This part is crucial because it helps you decide what to fix. Here’s a simple way to approach it:
- Compare Data: Look at the current vibration data and compare it with past data. Notice any changes? That’s your first clue.
- Check the Machine: Inspect the machine physically. Sometimes, the issue is visible, like a loose bolt or worn-out part.
- Consult Manuals: Use the machine’s manual to understand what certain vibrations might mean. Manufacturers often provide this info.
- Seek Expert Help: If you’re still unsure, ask an expert. Sometimes, a second pair of eyes can catch something you missed.
Last year, I was working on a project where the machine had unusual low-frequency vibrations. After following these steps, we found out it was due to a misaligned shaft. Simple fix, but it saved us from bigger problems down the line.
So there you have it! Interpreting vibration data isn’t as daunting as it seems. With practice, you’ll get better at spotting patterns and diagnosing issues. Just remember, every piece of data is a clue to solving the puzzle of your machine’s health.
Expert Tips For Accurate Measurement
Measuring vibration in mechanical systems requires precision and expertise. Accurate measurements can help in diagnosing issues, improving performance, and extending the lifespan of machinery. Here are some expert tips to ensure you achieve precise and reliable vibration measurements.
Avoiding Common Mistakes
Avoid loose sensors. They can give inaccurate readings. Always secure sensors properly to the machine.
Use the correct type of sensor for your specific application. Different machines need different sensors.
Do not ignore environmental factors. Temperature and humidity can affect measurements.
Ensuring Reliable Results
Calibrate your equipment regularly. This ensures that your readings are accurate.
Record measurements at the same time each day. This helps in comparing data accurately.
Analyze the data correctly. Use proper software and tools to interpret the results.
Keep detailed records. Document every measurement and any changes made to the machine.
Train your staff. Make sure everyone understands how to use the equipment properly.
Frequently Asked Questions
How Do You Measure Vibration In A Machine?
Use a vibration meter or accelerometer to measure machine vibration. Attach the sensor to the machine and record readings.
What Unit Of Measure Is Used For A Mechanical Vibration?
Mechanical vibration is measured in units like Hertz (Hz) for frequency, meters per second squared (m/s²) for acceleration, and micrometers (µm) for displacement.
What Are The Methods Of Vibration Test?
Vibration test methods include sine sweep, random vibration, shock testing, and resonance search. These assess product durability and performance.
What Instrument Measures Vibration?
A vibrometer or accelerometer measures vibration. These instruments detect and analyze vibrations in various settings.
Conclusion
Accurately measuring vibration is key to maintaining mechanical systems. Regular checks prevent equipment failures. Use proper tools and follow guidelines. Consistent monitoring ensures smooth operation. Invest in quality devices for reliable readings. Analyze data to spot issues early. Address problems before they escalate.
Keep your machinery in top shape. Simple steps lead to long-term benefits.