Measuring stress and strain in materials is crucial for understanding their behavior under load. Accurate measurements ensure the safety and durability of structures.
Stress and strain analysis helps engineers determine how materials will perform in different conditions. Stress refers to the force applied to a material, while strain measures the deformation resulting from this force. Knowing how to measure these factors is essential for designing safe and efficient structures.
This blog will guide you through the methods and tools used to measure stress and strain, providing a clear understanding of each step involved. By the end, you will know how to assess material performance accurately and ensure structural integrity in your projects.
Introduction To Stress And Strain
Hey friends, today I want to talk about something really important – stress and strain in materials. Why? Because it helps us understand how materials behave under different conditions. Think about a rubber band. When you pull it, it stretches. If you pull too hard, it breaks. This is what engineers and scientists study to make sure buildings, bridges, and even airplanes stay safe and sound. So, let’s dive into it!
Definition Of Stress
First, let’s talk about stress. No, not the kind you feel before exams! Stress in materials is the force that is applied to a material, divided by the area it’s applied on. Imagine you are pushing on a door. The harder you push, the more stress you are putting on it. In simple words, stress is a measure of how much force is acting on a material.
Type of Stress | Description |
---|---|
Tensile Stress | Pulling force |
Compressive Stress | Pushing force |
Shear Stress | Sliding force |
Definition Of Strain
Now, let’s move on to strain. Strain is what happens to a material when stress is applied. It’s the change in shape or size of the material. Think about our rubber band again. When you pull it, it gets longer. This change in length is strain. It’s a way to measure how much a material deforms under stress.
- Tensile Strain: Stretching or lengthening
- Compressive Strain: Squishing or shortening
- Shear Strain: Bending or sliding
Understanding stress and strain is like understanding the relationship between effort and result. The effort (stress) you put on a material causes a result (strain). Knowing how materials respond helps us design things that can handle different forces without breaking.
I hope this makes stress and strain a bit clearer for you. Remember, it’s all about how materials handle force and change shape. This knowledge is key for building safe structures and making sure our everyday items work well. Stay tuned for more tips on understanding materials!
Types Of Stress
Hey friends, ever wondered how engineers measure stress in materials? It’s like figuring out how much weight a bridge can hold before it breaks. Different types of stress can act on materials, and each type affects the material in a unique way. Let’s dive into the common types of stress: tensile, compressive, and shear stress.
Tensile Stress
Tensile stress is when a material is being pulled apart. Imagine you’re pulling on both ends of a rubber band. The force you’re applying is tensile stress. This type of stress tries to stretch the material. Engineers often use tensile stress tests to see how much a material can stretch before it breaks.
- Example: Stretching a piece of metal until it snaps.
- Use: Testing materials like steel cables or ropes.
Compressive Stress
Compressive stress is the opposite of tensile stress. Instead of pulling, you’re pushing. Picture squeezing a sponge. The force you’re applying is compressive stress. This type of stress tries to shorten the material. Engineers test compressive stress to see how much a material can be compressed before it deforms or breaks.
- Example: Crushing a can of soda.
- Use: Testing materials like concrete or brick.
Shear Stress
Shear stress happens when forces act parallel to a material’s surface. Imagine sliding a deck of cards. The cards slide over each other because of shear stress. This type of stress tries to make parts of the material slide past each other. Engineers check for shear stress to ensure materials can handle sliding forces without breaking.
- Example: Cutting paper with scissors.
- Use: Testing materials in structures like beams or bolts.
Understanding these types of stress helps engineers make safer, stronger, and more reliable products. Next time you stretch a rubber band, crush a can, or cut paper, remember you’re applying different types of stress!
Types Of Strain
Understanding the types of strain is crucial in material science. Strain refers to the deformation of a material due to applied stress. It helps in predicting material behavior under various conditions. Strain can be classified into two main types: elastic strain and plastic strain.
Elastic Strain
Elastic strain is a temporary deformation of a material. This type of strain occurs when the material returns to its original shape after removing the stress. Think of a rubber band. Stretch it, and it goes back to its original form. Elastic strain follows Hooke’s Law, which states that strain is proportional to stress within the elastic limit.
Plastic Strain
Plastic strain is a permanent deformation. This occurs when the material does not return to its original shape after removing the stress. Imagine bending a paperclip. It stays bent even after you release it. Plastic strain happens when the applied stress exceeds the material’s yield strength. It leads to permanent changes in the material’s structure.
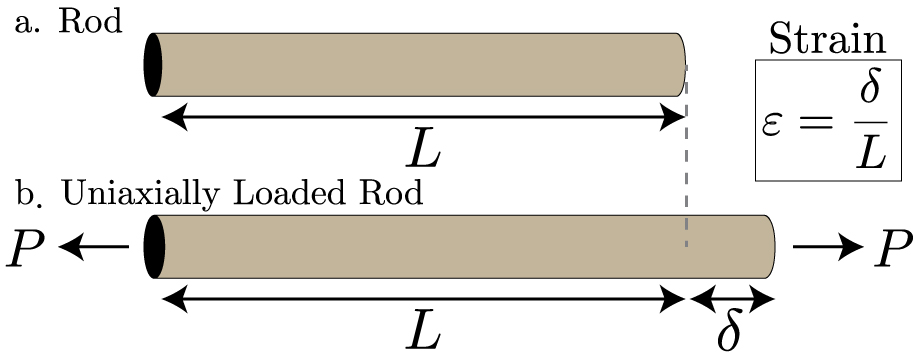
Credit: www.bu.edu
Stress-strain Relationship
The stress-strain relationship in materials is crucial for understanding their mechanical properties. Engineers and scientists measure stress and strain to predict how materials will behave under different forces. This knowledge helps in designing safe and efficient structures.
Hooke’s Law
Hooke’s Law describes the linear relationship between stress and strain. According to this law, stress is directly proportional to strain within the elastic limit. This means that the material will return to its original shape when the force is removed.
Mathematically, Hooke’s Law is expressed as σ = Eε, where σ is stress, E is the modulus of elasticity, and ε is strain. This simple equation helps predict how materials will deform under various loads.
Stress-strain Curve
The stress-strain curve provides a graphical representation of a material’s behavior under stress. The curve typically has several distinct regions. The initial linear portion represents elastic deformation, where Hooke’s Law applies. Beyond this region, the material experiences plastic deformation.
The yield point marks the transition from elastic to plastic deformation. Beyond the yield point, the material will not return to its original shape. The curve continues to rise until it reaches the ultimate tensile strength. This is the maximum stress the material can withstand before breaking.
Understanding the stress-strain curve is essential for material selection and design. It helps engineers determine the safe working limits of materials and avoid catastrophic failures.
Measuring Instruments
Understanding stress and strain in materials is crucial. Accurate measurements require reliable instruments. These tools help in assessing how materials deform under stress.
Two primary instruments are strain gauges and extensometers. Each has its unique application and method. Let’s explore these essential tools for measuring stress and strain in materials.
Strain Gauges
Strain gauges measure the strain on an object’s surface. They consist of a thin foil pattern attached to the material. When the material deforms, the foil pattern also deforms. This change causes a measurable resistance change in the gauge.
Strain gauges are simple and cost-effective. They provide accurate readings for small deformations. Engineers use them in various fields, including aerospace and civil engineering. Strain gauges are ideal for monitoring structural health and ensuring safety.
Extensometers
Extensometers measure the change in length between two points on a material. They are highly precise and can measure even minor deformations. Extensometers have two main types: contact and non-contact.
Contact extensometers physically attach to the material. They use mechanical or electronic systems to measure changes. Non-contact extensometers use lasers or cameras. These tools capture accurate measurements without touching the material.
Extensometers are essential in tensile testing. They provide data on material behavior under various loads. This information helps in designing safer and more efficient structures.
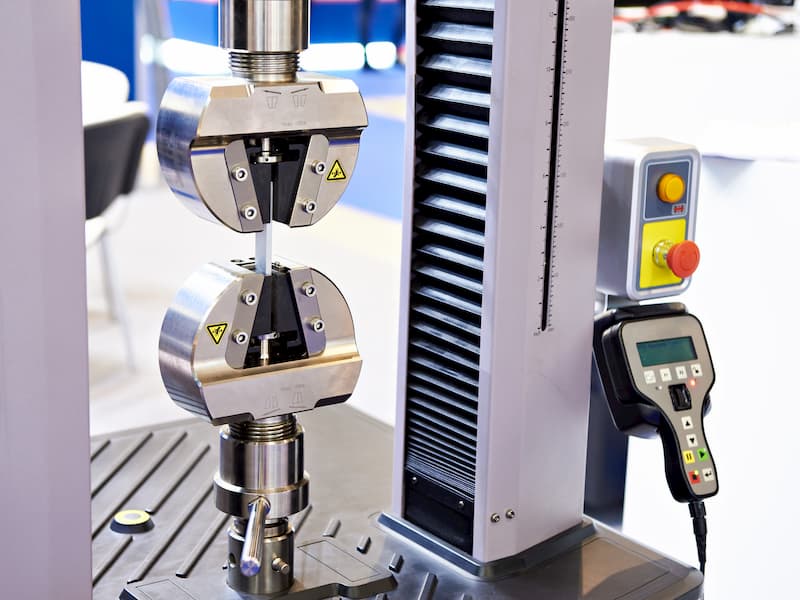
Credit: fractory.com
Experimental Methods
Hey there! Today, we’re diving into how to measure stress and strain in materials. This is super important because it helps us understand how materials behave under different forces. We’ll focus on three common experimental methods: tensile testing, compression testing, and bending testing. These methods are like the detective tools engineers use to figure out how strong and flexible a material is.
Tensile Testing
First up, let’s talk about tensile testing. Imagine pulling a piece of taffy. You stretch it to see how far it can go before it snaps. That’s basically what tensile testing is all about. In this test, a material sample is pulled apart until it breaks. This helps us measure how much force the material can handle before it fails.
The setup is pretty simple:
- A sample of the material is clamped at both ends.
- A machine pulls the sample with increasing force.
- We measure the force and the amount of stretch.
For example, let’s say you have a piece of metal. You want to know if it can hold up under heavy loads. Tensile testing will tell you how strong that metal is and how much it can stretch before it gives up.
Compression Testing
Next, we have compression testing. This is like squeezing a sponge to see how much it compresses. Instead of pulling, we push the material to see how it reacts. This test is essential for materials that will experience loads pushing on them, like columns in a building.
Here’s how it works:
- A sample is placed between two plates.
- The plates push together, compressing the sample.
- We measure the force and how much the sample shortens.
Think of a foam block. When you press it, you want to know how much it squishes and if it can bounce back. Compression testing gives you these answers.
Bending Testing
Finally, let’s look at bending testing. Picture bending a ruler to see how much it can flex before it snaps. This test shows us how a material behaves when a force is applied in the middle, causing it to bend.
The process involves:
- Placing the material sample on two supports.
- Applying a force in the middle of the sample.
- Measuring the force and the amount of bend.
For instance, if you’re designing a bridge, you want to know if the beams can handle the weight of cars driving over them. Bending testing will help you understand how much the beams can flex without breaking.
These experimental methods are vital in material science. They help us ensure safety and reliability in everything from buildings to bridges. So next time you see a skyscraper or drive over a bridge, remember, these tests made it possible!
Data Analysis
Data analysis is crucial in understanding stress and strain in materials. Accurate analysis helps predict material behavior. It aids in improving safety and performance. Below, we explore how to interpret stress-strain data and calculate modulus of elasticity.
Interpreting Stress-strain Data
Stress-strain data comes from testing materials under load. This data shows how materials react to different forces. It includes two main parts: stress and strain. Stress is the force applied per unit area. Strain is the material’s deformation in response to stress.
Plot the data on a stress-strain curve. The curve’s shape reveals important information. The initial straight line indicates elastic behavior. The material returns to its original shape after removing the load. The curve’s slope changes as the material enters the plastic region. Here, permanent deformation occurs.
Identify key points on the curve. The yield point marks the end of elastic behavior. The ultimate tensile strength is the maximum stress the material can withstand. The fracture point indicates where the material breaks.
Calculating Modulus Of Elasticity
The modulus of elasticity measures a material’s stiffness. It is also known as Young’s modulus. Calculate it from the stress-strain curve’s initial linear region. This part represents elastic behavior.
Use the formula: Modulus of Elasticity (E) = Stress / Strain. Measure stress and strain values from the linear region. Divide stress by strain to find the modulus. A higher modulus indicates a stiffer material. Lower values mean the material is more flexible.
Understanding these calculations aids in material selection. It ensures materials meet specific performance requirements. Accurate data analysis improves safety and efficiency in various applications.
Applications
Understanding the applications of stress and strain measurement is crucial. Knowing how materials respond under various conditions helps in many fields. Engineers use this information to make informed decisions.
Engineering Design
In engineering design, measuring stress and strain is essential. It helps predict how materials will behave under load. This prediction ensures safety and reliability. Engineers can design structures that withstand different forces. Buildings, bridges, and machinery all benefit from this knowledge.
Accurate measurements prevent failures. They help in optimizing materials used in construction. This leads to cost-effective designs without compromising strength. Engineers can also explore new materials with better performance.
Material Selection
Choosing the right material is vital in any project. Stress and strain measurements guide this process. Materials must meet specific criteria for strength, flexibility, and durability. These measurements provide the needed data.
For example, in aerospace, materials must handle high stress and temperature. In electronics, materials need to be flexible and lightweight. By understanding stress and strain, engineers select the best materials. This ensures the final product performs as expected.
Overall, stress and strain measurements are key in multiple applications. They enhance design, safety, and efficiency across various industries.
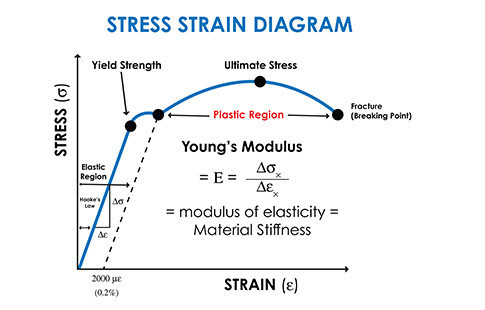
Credit: www.micro-measurements.com
Frequently Asked Questions
How Are Stress And Strain Measured?
Stress is measured using a load cell or force gauge. Strain is measured with a strain gauge, which detects deformation.
How Do You Calculate Stress And Strain Of A Material?
Calculate stress by dividing force by the material’s cross-sectional area. Calculate strain by dividing the change in length by the original length.
Can You Measure Stress In A Material?
Yes, you can measure stress in a material using devices like strain gauges or through methods such as X-ray diffraction.
What Equipment Is Used To Measure Stress Strain?
A universal testing machine measures stress and strain. Extensometers are used for precise strain measurements.
Conclusion
Measuring stress and strain in materials is crucial for safety. Use the right tools. Understand the material properties. This ensures accurate measurements. Apply these methods consistently. Track changes over time. This helps in predicting failures. Always prioritize accuracy and safety.
Stay informed about new techniques. This knowledge keeps your projects safe and reliable.